SPARE PARTS PREDICTION WITH MICROSOFT AZURE
INDUSTRY
Manufacturing
CLOUD PROVIDER
Microsoft Azure
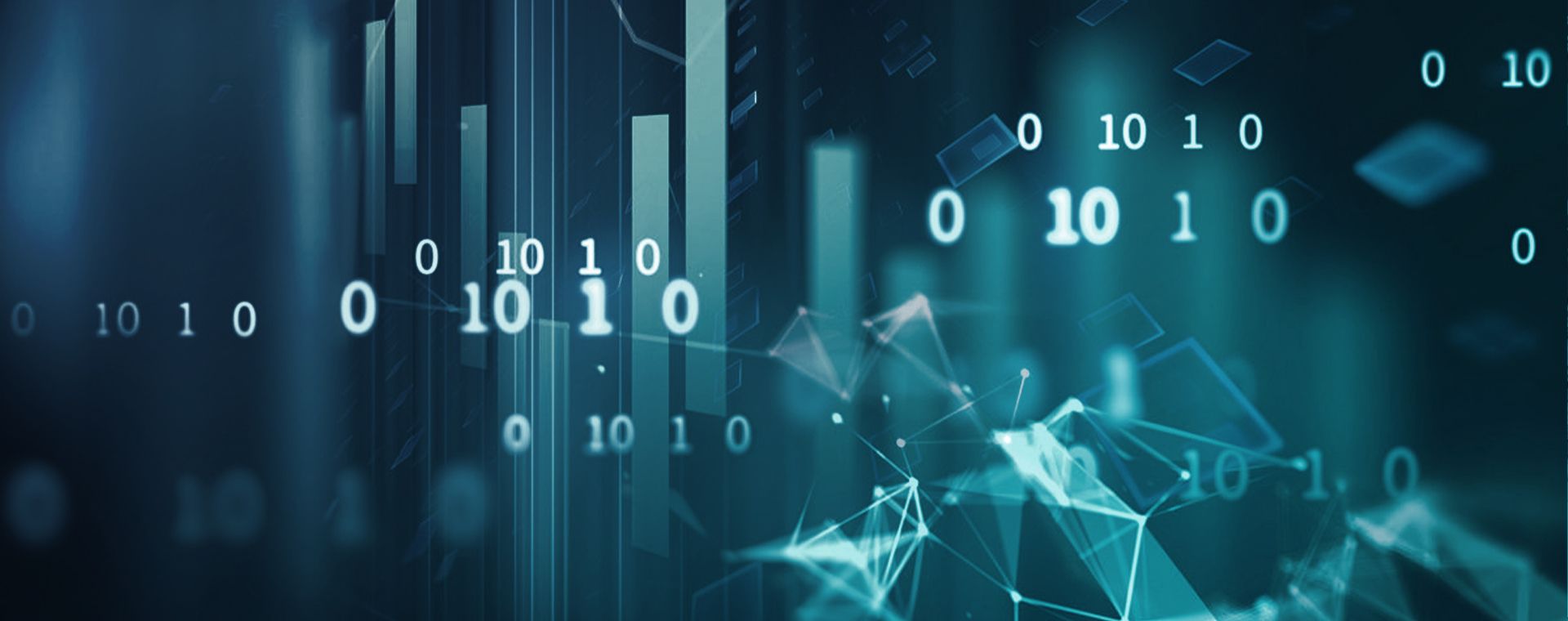
What effect does it have when machine learning and spare parts management go hand in hand? And how can existing data based on SAP, for example, be profitably used and optimized in the logistics industry?
Zoi was asked to optimize the spare parts planning of a large medium-sized Manufacturing company through machine learning. What we achieved was a 15% reduction in warehouse volume while maintaining the same level of service. All this was reached by adapting procedures specifically geared to our client's domain, setting up a data-based test phase, developing a suitable serverless data processing strategy, and implementing the new service. But first things first…
This is a paragraph. Writing in paragraphs lets visitors find what they are looking for quickly and easily.
This is a paragraph. Writing in paragraphs lets visitors find what they are looking for quickly and easily.
This is a paragraph. Writing in paragraphs lets visitors find what they are looking for quickly and easily.
This is a paragraph. Writing in paragraphs lets visitors find what they are looking for quickly and easily.
SPARE PARTS INVENTORY REDUCED BY 15%
LOGISTICS FORECASTS INTEGRATED WITH SAP ERP
ML ALGORITHMS USED TO CREATE FORECASTS FOR LOGISTICS
KNOW YOUR DATA: RELIEVE EMPLOYEES AND REDUCE STOCK
Many medium-sized companies face the same problem: Manufacturing companies produce an ever-increasing variety of devices and accessories with more and more configurations. This includes an ever-increasing volume of parts. At the same time, service and reaction time play an ever greater role for customers. However, many Manufacturing companies face the planning of inventories and orders with classical, sometimes even dusty processes and methods. This leads to an ever-increasing workload for employees, full warehouses, and ultimately an unnecessarily high capital binding.
Our customer had a clear requirement to reduce the stock of approximately 75,000 spare parts. Due to the high number of parts, it was clear from the beginning that an optimization of the existing processes could only be achieved by advanced automation of the same caliber.
After ensuring that relevant data was available and that a positive return on investment (ROI) was very likely to be expected at the end of the evaluation, a data-scientific metric was created on the basis of existing logistics KPIs in the company; this formed the basis of the training and the evaluation of the machine learning algorithms. The algorithms learn on the basis of historical data and take seasonal factors, material criteria, and other information into account. All this is essential to make the accuracy of the predictions even more accurate. For this purpose, we have created a system that combines modern deep-learning algorithms with established statistical methods. The result? The algorithm calculates at a particular time the probability that a certain quantity of parts will be needed at a certain location in the company's logistics network.
Through our method, the company gained a better forecast as well as a deeper understanding of the consumption of parts and the factors that influence deviations. All this helps to identify and combat potential sources of fire early on. As a result, problems in the processes can be quickly detected and remedied; likewise, potentially occurring negative scenarios can be proactively diagnosed thanks to the data obtained. This not only enables greater flexibility but also helps to minimize storage volume and the associated capital commitment.
UPGRADE YOUR DATA: TRANSLATE THE CUSTOMER'S LANGUAGE INTO AN APPLIED ALGORITHM
In the beginning, our team started with the data review and a feasibility analysis based on the data set that had been worked out. It quickly became clear that a high added value could be achieved compared to the planning strategy used at that time. On average, approximately 50,000 stock movements are carried out per day in warehouses of the size of the customer's warehouse. Parts are ordered, assembled, and shipped – everything is constantly in motion. The systems used for this are often outdated. Nevertheless, they still represent an investment for the company and cannot simply be switched off or replaced – especially since most employees have already internalized the processes. However, these systems offer the advantage that they contain all the data needed to optimize warehouse processes in a budget-friendly way.
CODE WITH YOUR DATA: TAILOR-MADE DATA ANALYSIS MEETS INDIVIDUAL CLOUD SOLUTION
In several sprints, the data sets collected were evaluated and the procedures were further refined until an optimal service level was achieved with minimum inventory. With this solution, the spare parts inventory can be reduced by up to 15% with the same service level. The new logistics forecast was then integrated into the customer's existing SAP ERP and BW systems. This protects the investment with respect to the existing systems and reduces the effort of process integration.
The training data set, which goes back many years, and the applied machine learning algorithms required considerable computing capacities for a run-through. However, since planning takes place in weekly cycles, the cloud offers suitable computing resources on demand. These are cost-effective to operate, scalable, and available serverless. For this reason, our solution runs in the customer's Virtual Private Cloud (VPC). This means that the company data does not leave the cloud data center. This corresponds exactly to the customer's security needs with regard to the processing of critical process data worthy of protection. The implementation was done in Microsoft Azure.
The technical solution is based on both statistical methods and deep learning for time series analysis. The algorithms we developed represent the state-of-the-art in the logistics industry. Similar methods are developed and used in the warehouses of Amazon and Zalando, among others. The building blocks are packaged within modern container technology using dockers and Kubernetes and are hosted on serverless environments in the cloud. The algorithms were implemented in Apache MXNet, a deep learning framework, and in the data science tools in Python.
How forecasting algorithms can help manage stock.
How the SAP systems and the customer’s data platform on Azure work together.
The path from preparing the data to the solution.
Often the systems already in use, such as SAP, provide all the data needed to further optimize warehouse processes in a budget-friendly manner.
The algorithms we have built up not only enable greater flexibility in inventory management but also help to minimize storage volume and the associated capital commitment.
CAROUSEL FILTER SETUP
CASES
Here are a few examples of how we have successfully supported our Manufacturing customers.
This is a paragraph. Writing in paragraphs lets visitors find what they are looking for quickly and easily.
This is a paragraph. Writing in paragraphs lets visitors find what they are looking for quickly and easily.
This is a paragraph. Writing in paragraphs lets visitors find what they are looking for quickly and easily.
This is a paragraph. Writing in paragraphs lets visitors find what they are looking for quickly and easily.
LET’S EXCHANGE IDEAS
Because you could change direction much faster than you think.